Developed in the Alps – produced in Asia.
James Noh has been in the paragliding business for a long time. He began in the 1990s with the South Korean paraglider manufacturer « Edel« .
First-generation paraglider pilots still remember the brand with the distinctive eagle beak logo. At the best of times, Edel was the leading manufacturer – but after several ups and downs, Edel disappeared from the scene. When the Edel brand failed at the beginning of the new millennium, James Noh started his own production in South Korea with some of the former Edel workers and machines. Later, James decided to move the company to Thailand because of the better economic environment. There he started to produce for some paraglider brands. Since the joint venture with skywalk, James as a producer has a high degree of planning security and skywalk has a reliable production with which to break new ground – a win-win situation for both! Together we are looking forward to designing and manufacturing many more innovative products for our pilots!
Designing paragliders is one thing – producing them is another.
For the large and small brands that, with a few exceptions, are based in the Alps, highly specialized companies manufacture paragliders, reserve chutes and harnesses. To become independent of supply bottlenecks and to achieve the best possible quality, skywalk has established an exclusive joint venture.
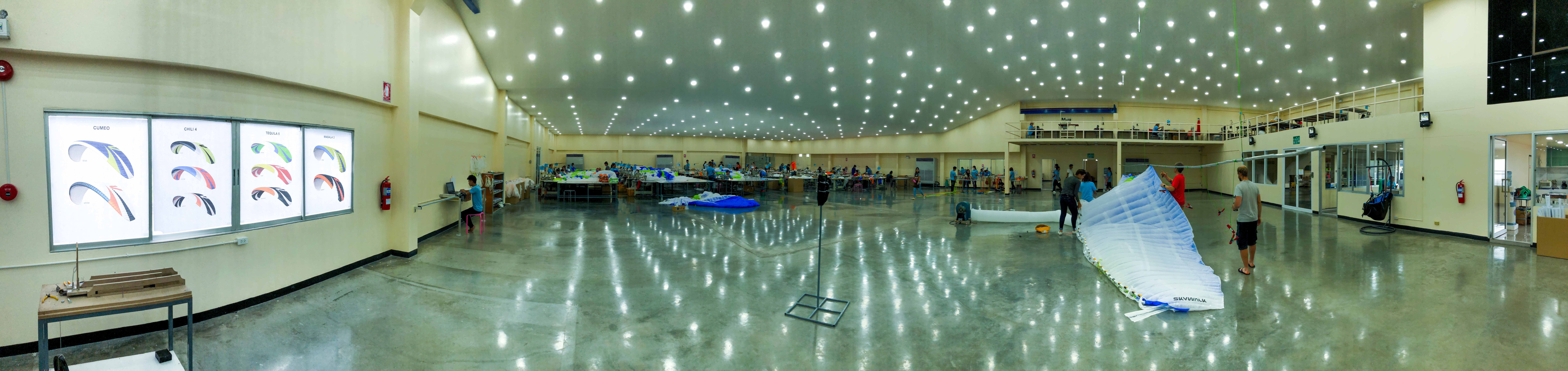
Chon Buri. A name that sounds like an idyllic seaside resort in Asia. In fact, the town of 30,000 inhabitants on the Gulf of Thailand is a bustling industrial town where many companies produce for the world market. One of them is « Acrocross« , or more precisely « Acrocross skywalk », a textile factory specializing in the production of paragliders. Here, around 180 employees manufacture paragliders, reserve chutes and, for some time now, harnesses, exclusively for skywalk. The head of the company is the 52-year-old South Korean James Noh, who has more than 30 years of experience in the production of aviation sports equipment. James came here a few years ago from his home country of South Korea, because in his view Thailand is the best place for the complex and sometimes quite turbulent production process.
Arne Wehrlin, head of skywalk Paragliders, explains how the joint venture came about: « Since skywalk was founded, we, like most other manufacturers, have had our gliders sewn by different production companies. The know-how for this has long since been in Asia, and this has not only to do with labor costs. In recent years, we have had more and more products produced at James Noh’s company. We then quickly realized that we actually had similar interests. James was looking for more planning security and we wanted our own production! » In 2018 the time had come, the cooperation between Acrocross and skywalk was deepened with a joint venture and Acrocross/skywalk was founded. For this purpose, a new company site was built in Chon Buri, a ten-minute drive from James Noh’s other company « OEM-Acrocross », where he works as a contractor for other brands.
Joint venture between Acrocross and skywalk
During the construction of the production facility, skywalk was able to perfectly implement the framework conditions for modern paraglider construction. The rooms are bright, friendly – and air-conditioned. This not only benefits working conditions for the staff, but is also a prerequisite for consistent product quality. Storage and processing of materials at the same humidity and temperature are essential to eliminate tolerances in the manufacture of the wings, which are designed 10,000 kilometers away. Since the production line only works for one manufacturer, errors, for example when retooling a machine, are almost impossible. All steps follow certified processes, exclusively from skywalk for skywalk. Today, a paraglider production plant is much more than a sewing shop where aviation products are simply assembled. The production is high-tech, and each model has specific features that have to be implemented. Complex but essential is the adherence to sewing tolerances in the millimeter range, to produce the tension ratios accurately and in conformity with development. Every single part in the production has an influence on the material cut developed in the 3D program, which affects handling, performance and finally safety.
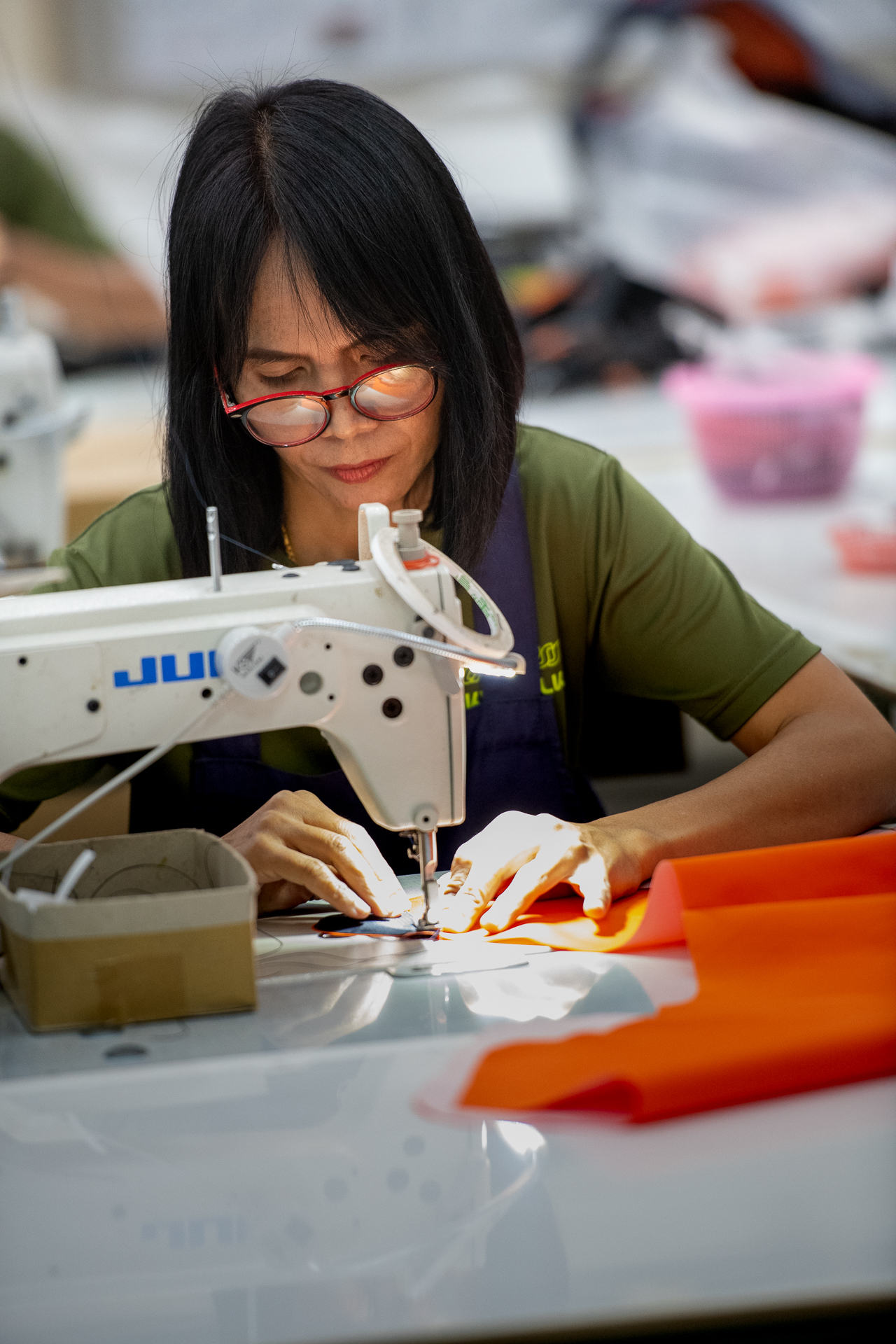
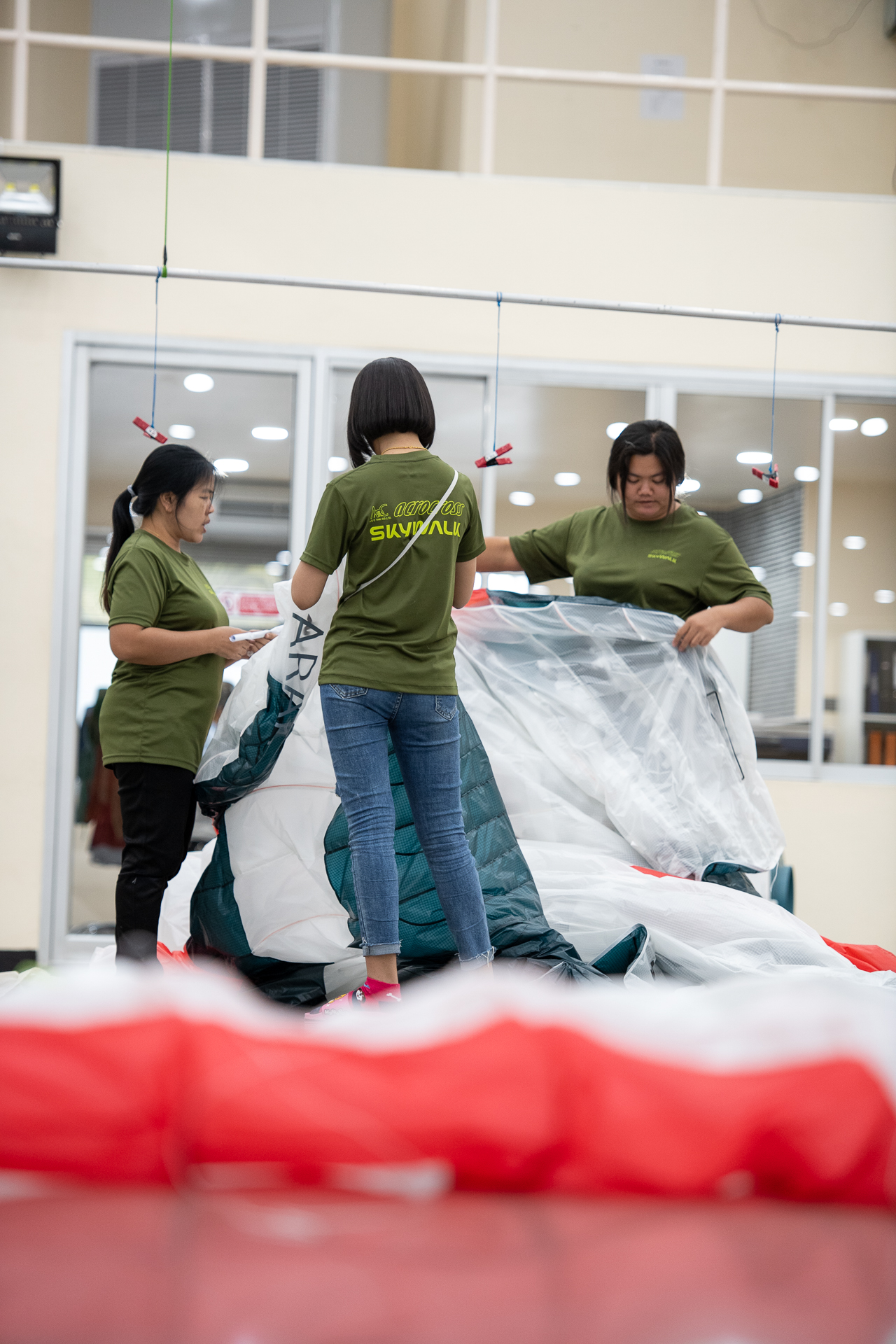
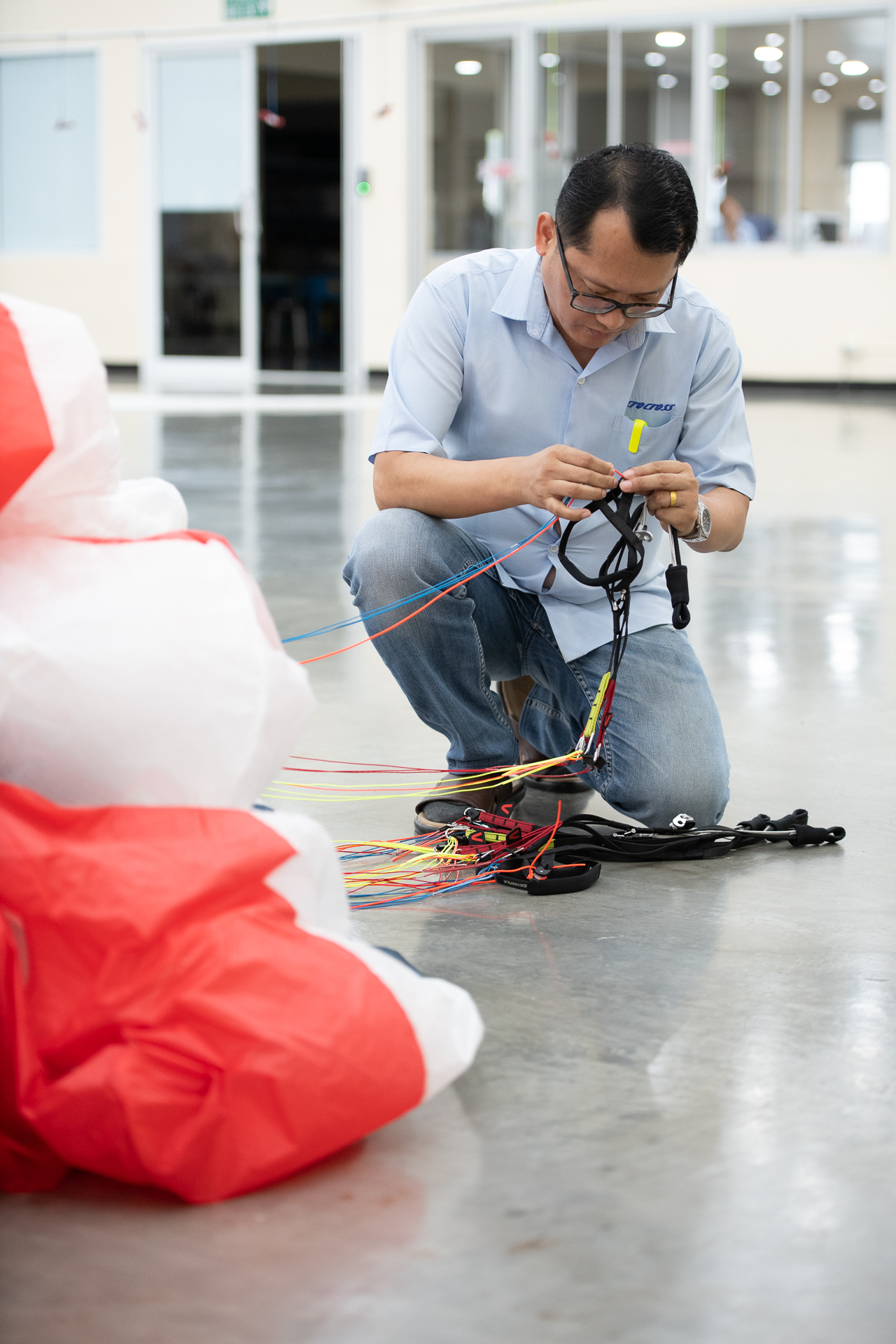
Because the production is exclusively for skywalk, the specifications of the development team can be implemented exactly. To train production staff, the R&D team flies to Thailand several times a year. James is the most important link between the R&D team and the employees on site. Thanks to his experience, he knows exactly how to implement the smallest development details on the finished product…