In den Alpen entwickelt – In Asien produziert.
James Noh ist schon lange im Gleitschirmbusiness. Sein Einstieg begann in den Neunzigern des vergangenen Jahrhunderts beim südkoreanischen Gleitschirmhersteller „Edel“.
Als die Marke Edel am Anfang des neuen Millenniums scheiterte, startete James Noh in Südkorea mit einigen der ehemaligen Edel-Arbeiter und Maschinen eine eigene Produktion. Später entschied sich James wegen des besseren wirtschaftlichen Umfelds für die Verlagerung des Unternehmens nach Thailand. Dort begann er für einige Gleitschirmmarken zu produzieren.
Seit dem Joint Venture mit skywalk hat James als Produzent eine hohe Planungssicherheit und skywalk eine verlässliche Produktion, mit der man neue Wege gehen kann – eine Win-win-Situation für beide! Gemeinsam freuen wir uns viele weitere innovative Produkte für unsere Piloten zu entwickeln und zu produzieren!
Gleitschirme zu entwickeln, ist die eine Sache – sie zu produzieren, eine andere.
Für die großen und kleinen Marken, die ihren Sitz bis auf wenige Ausnahmen im Alpenraum haben, fertigen deswegen hochspezialisierte Unternehmen Schirme, Rettungsgeräte und Gurtzeuge. Um sich unabhängig von Lieferengpässen zu machen und die bestmögliche Qualität zu erreichen, hat skywalk ein exklusives Joint Venture aufgebaut.
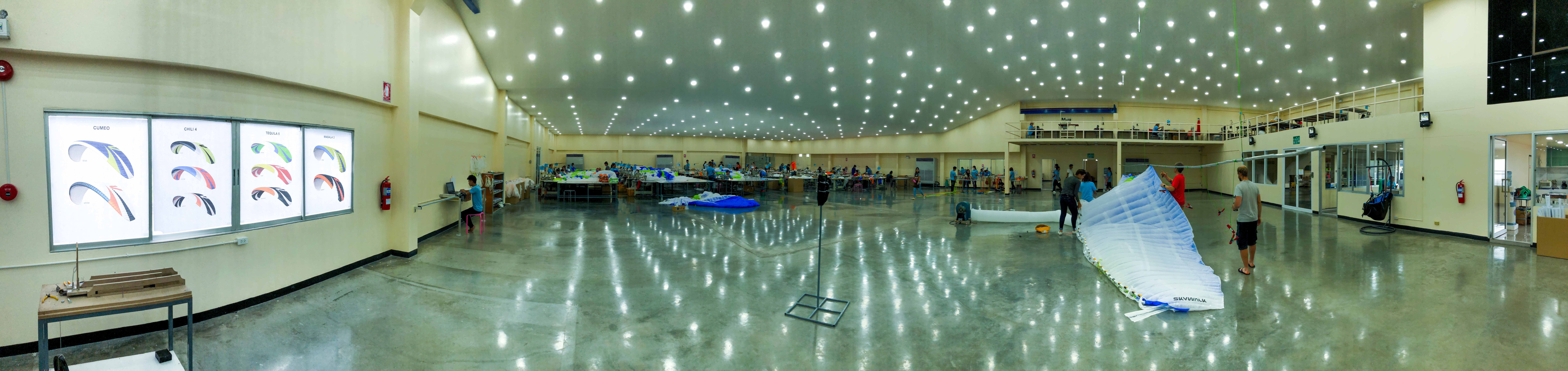
Chon Buri. Ein Name, der klingt wie ein idyllischer Badeort in Asien. Tatsächlich ist der 30.000-Einwohner-Ort am Golf von Thailand ein wuseliges Industriestädtchen, in dem viele Unternehmen für den Weltmarkt produzieren. Eines von ihnen ist „Acrocross“, genauer gesagt „Acrocross skywalk“, eine auf die Produktion von Gleitschirmen spezialisierte Textilfabrik. Rund 180 Mitarbeiter fertigen hier exklusiv für skywalk Gleitschirme, Rettungsgeräte und seit einiger Zeit auch Gurtzeuge. Kopf des Unternehmens ist der 52-jährige Südkoreaner James Noh, der über mehr als 30 Jahre Erfahrung in der Produktion von Flugsport-Equipment verfügt. James kam vor einigen Jahren aus seinem Heimatland Südkorea hierher, weil Thailand aus seiner Sicht der beste Platz für den komplexen und manchmal durchaus turbulenten Produktionsprozess ist.
Arne Wehrlin, Kopf von skywalk Paragliders, erzählt, wie es zu dem Joint Venture kam: „Seit der Gründung von skywalk haben wir unsere Schirme, wie die meisten anderen Hersteller, bei unterschiedlichen Produktionsbetrieben nähen lassen. Das Know-how dafür liegt mittlerweile längst in Asien, und das hat nicht nur mit den Lohnkosten zu tun. In den letzten Jahren haben wir immer mehr Produkte im Unternehmen von James Noh produzieren lassen. Wir haben dann schnell gemerkt, dass wir eigentlich deckungsgleiche Interessen haben. James war auf der Suche nach mehr Planungssicherheit und wir wollten eine eigene Produktion!“
2018 war es dann so weit, die Zusammenarbeit zwischen Acrocross und skywalk wurde mit einem Joint Venture vertieft und Acrocross/skywalk gegründet. Dazu wurde in Chon Buri ein neues Firmenareal aufgebaut, das zehn Autominuten von James Nohs anderer Firma „OEM-Acrocross“ entfernt liegt, wo er als Auftragnehmer für andere Marken arbeitet.
Joint Venture zwischen Acrocross und skywalk
Bei der Errichtung der Produktionsräume konnten die Rahmenbedingungen für einen modernen Gleitschirmbau perfekt umgesetzt werden. Die Räume sind hell, freundlich – und klimatisiert. Das kommt nicht nur den Arbeitsbedingungen für das Personal zugute, sondern ist Voraussetzung für eine gleichbleibende Produktqualität. Lagerung und Verarbeitung der Materialien bei gleicher Luftfeuchtigkeit und Temperatur sind essenziell, um Toleranzen beim Bau der Flügel auszuschließen, die 10.000 Kilometer entfernt konstruiert werden.
Da in der Produktionsstraße nur noch für einen einzigen Hersteller gearbeitet wird, sind Fehler, beispielsweise beim Umrüsten einer Maschine, nahezu ausgeschlossen. Alle Schritte folgen zertifizierten Prozessen, exklusiv von skywalk für skywalk. Ein Gleitschirm-Produktionsbetrieb ist heute längst mehr als eine Näherei, in der Flugsportprodukte einfach nur zusammengenäht werden. Die Fertigung ist Hightech, jedes Modell hat konkrete Besonderheiten, die umgesetzt werden müssen. Komplex, aber essenziell ist die Einhaltung der Nähtoleranzen im Millimeterbereich, um die Spannungsverhältnisse genau und Entwicklungskonform zu produzieren. Jedes einzelne Teil in der Fertigung hat Einfluss auf den im 3D Programm entwickelten Segelschnitt, der sich auf das Handling, die Leistung und nicht zuletzt auf die Sicherheit, auswirkt.
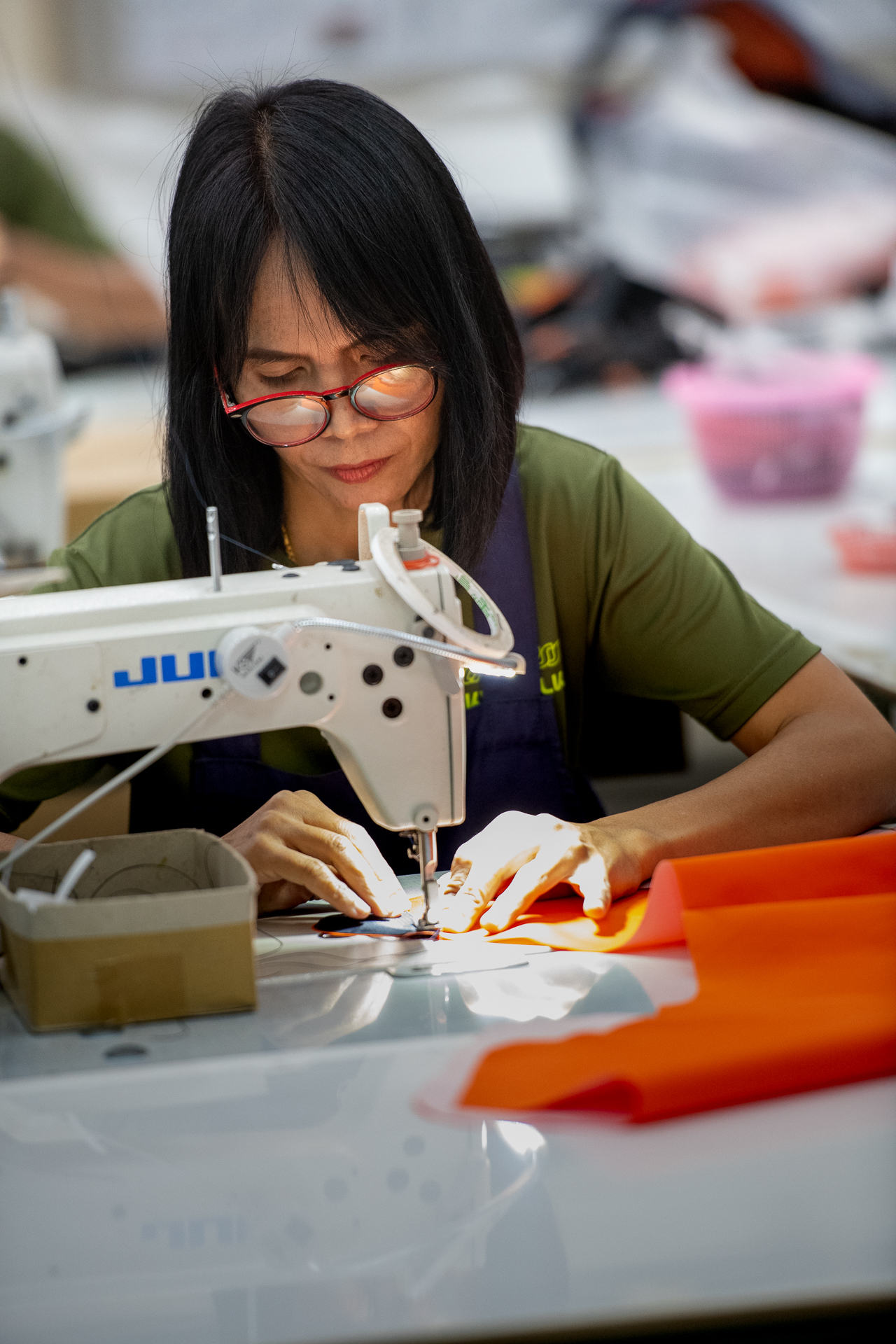
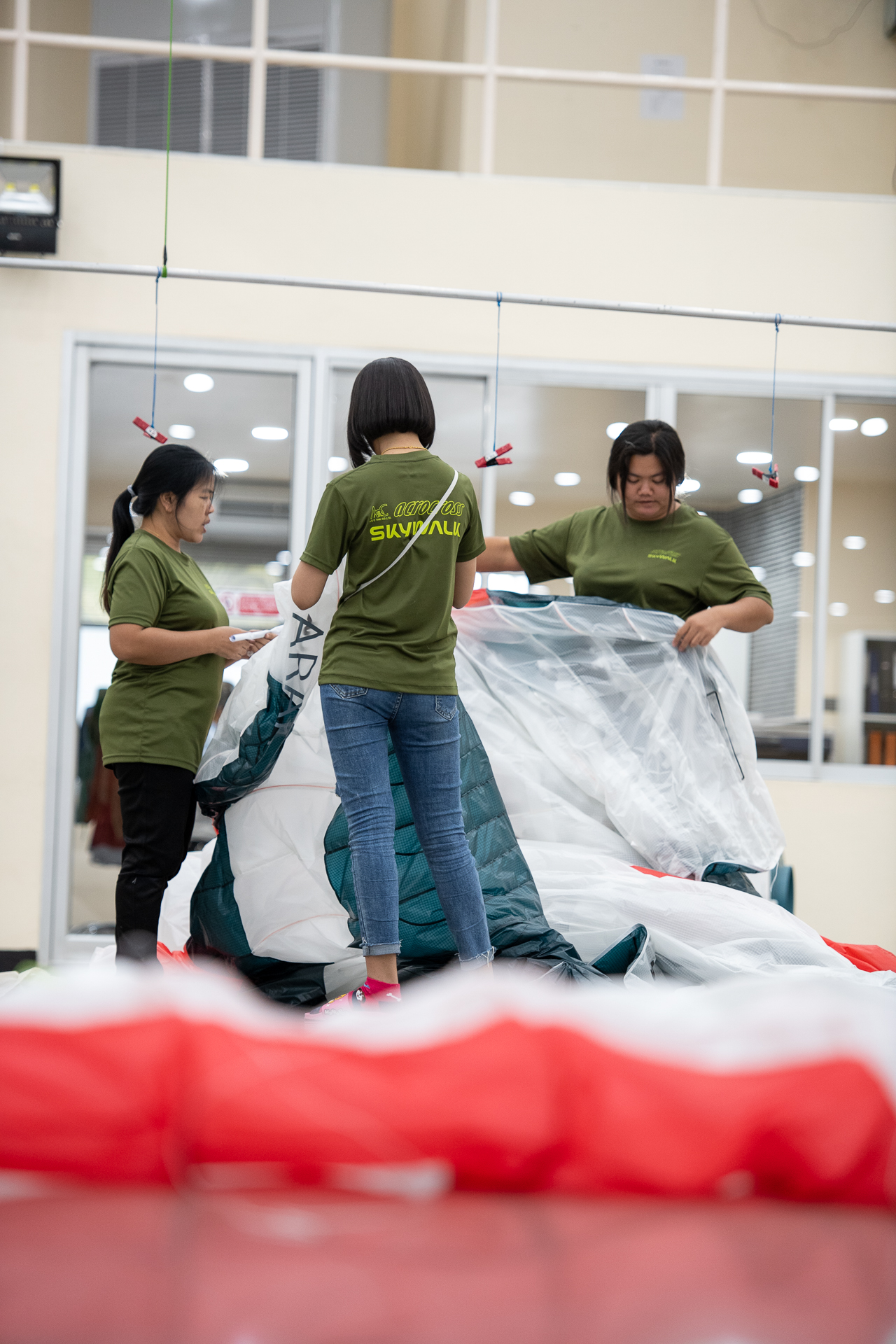
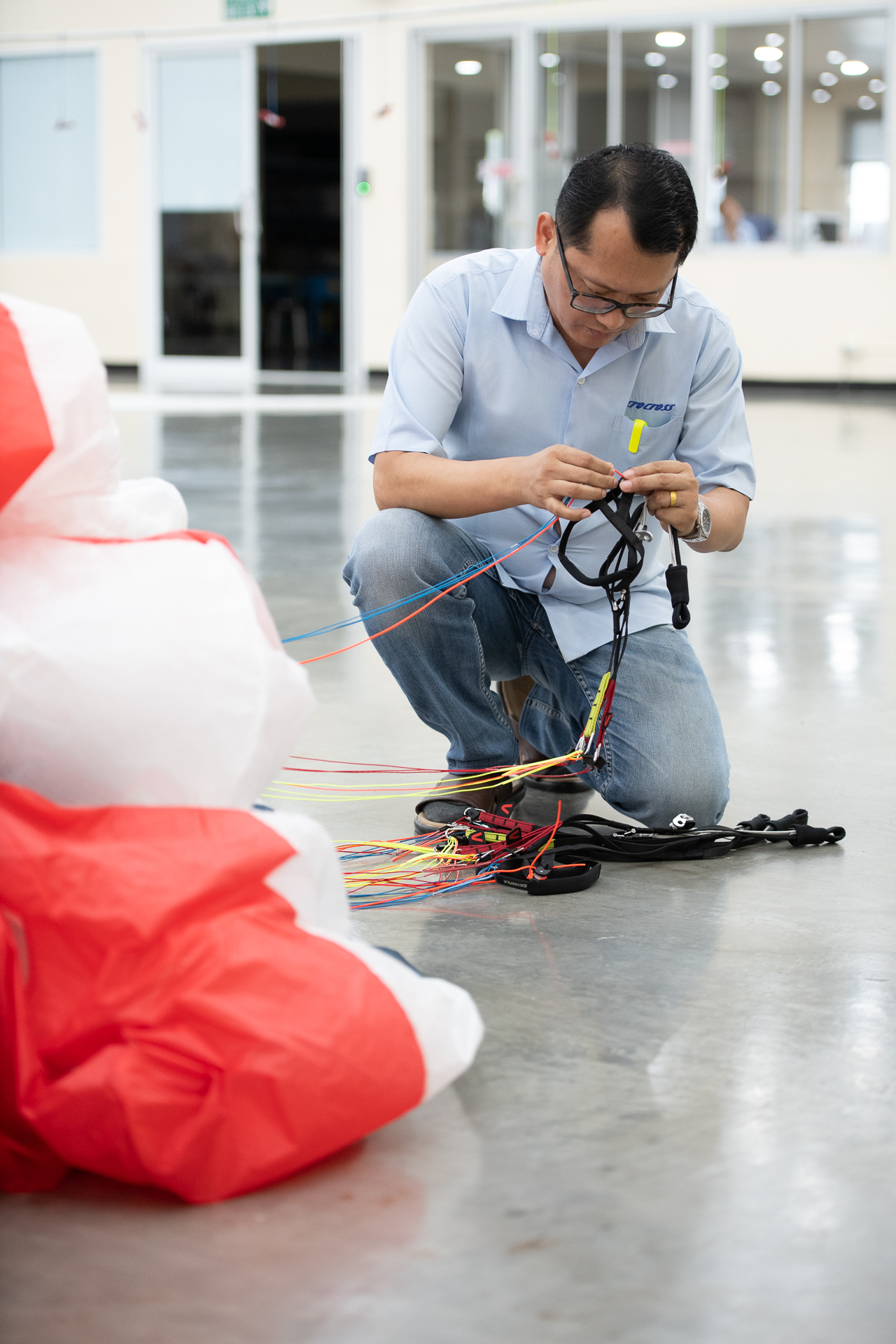
Da die Produktion rein auf skywalk abgestimmt ist, können die Vorgaben des Entwicklungsteams exakt umgesetzt werden. Um die Produktionsmitarbeiter zu schulen, fliegt das R&D Team mehrmals im Jahr nach Thailand. Dabei ist James das wichtigste Bindeglied zwischen dem R&D-Team und den Mitarbeitern vor Ort. Dank seiner Erfahrung weiß er genau, wie man kleinste Entwicklungsdetails am fertigen Produkt umsetzt …